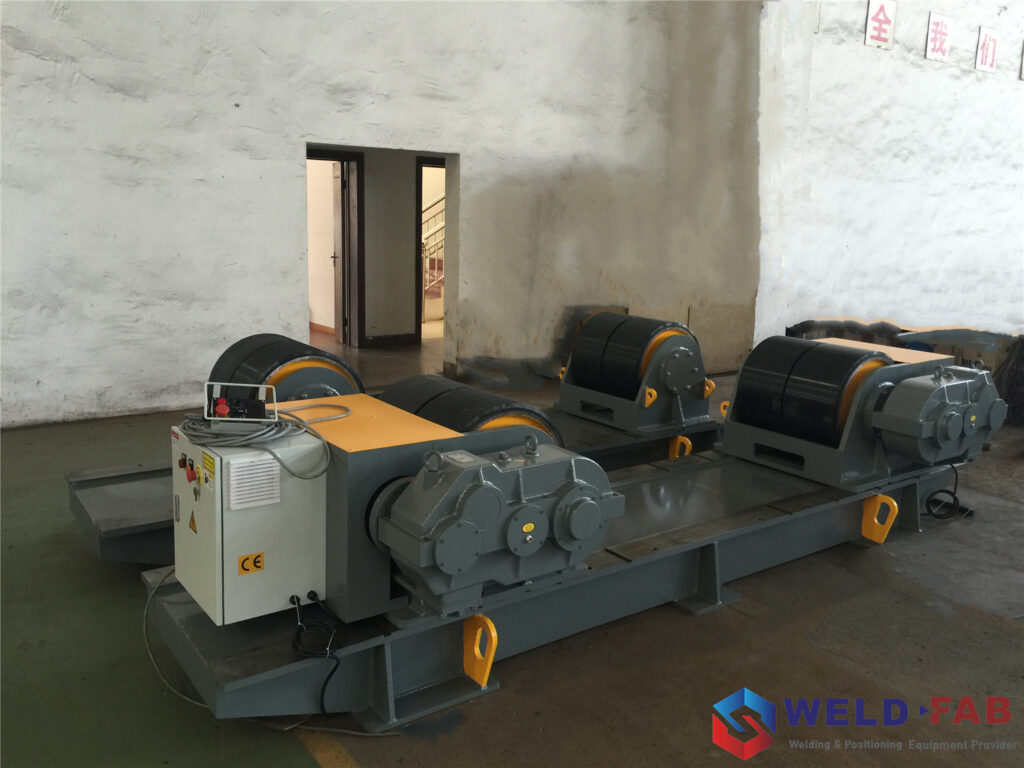
WELDING ROTATORS
WELD-FAB supply all kinds of welding rotators, including self-aligning type and conventional type. To learn more about fit-up rotators and anti drift rotators, please contact with our sales team.
* Loading capacity from 2Ton to 2000Ton
* Pipe diameter range from 150mm to 15,000mm
* Power supply customized from 110V to 600V
* Wheels material can be adopted Polyurethane, Metal and Rubber
* Mechanical structure can be design for Self-aligning, Conventional or Hydraulic type
Weld-Fab Welding Rotators
Self-aligning Welding Rotator
Conventional Welding Rotator
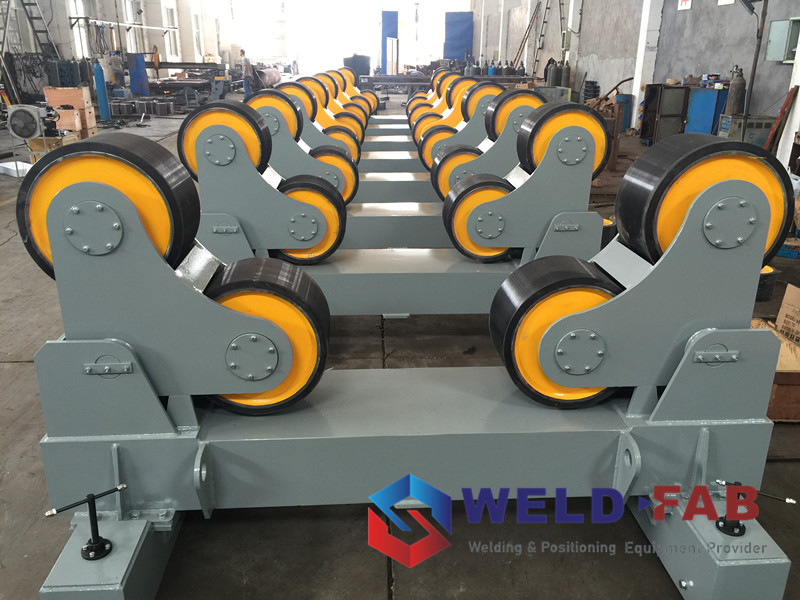
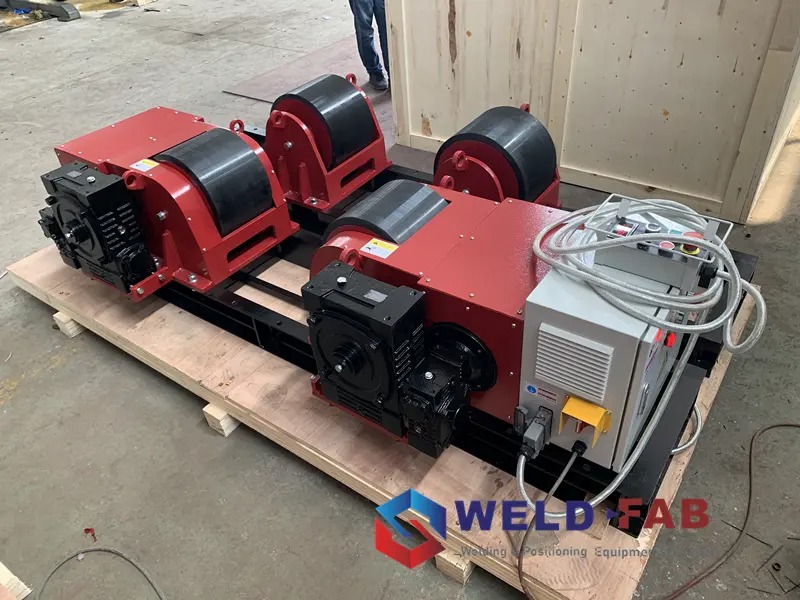
Weld-Fab Welding Rotator Video
Why Choose Weld-Fab Rotators?
√ Standard match with CSA & CUL and CE
√ Stable mechanical structure
√ Safety electrical design
√ Special customized loading capacity and dimension
√ Superior warranty and after service
Welding Rotator – The Comprehensive FAQ Guide
There are thousands, if not millions of welding rotators in the market today. But, if you are looking for the ones that can bring you the best value, you’re just in the right page!
For today’s guide, we’ll discuss all the information you need in figuring out what welding rotators are. Not only that, we will also be bringing you the best welding rotator supplier in the market today!
What is a Welding Rotator?
A welding rotator is just one of the many equipment you can use to make your welding processes easier.
Example of what a welding rotator looks like
Akin to positioners, welding rotators can help eliminate the need for your projects to have human intervention.
What they do basically is they rotate cylindrical vessels or any other type of workpiece with rounded sides.
Can You Make a DIY Welding Rotator?
Yes, many home welders are attempting to create and produce welding rotators from scratch.
A homemade or a DIY welding rotator without any additional parts
However, many people are confused in distinguishing between welding rotators and positioners. Welding positioners are the machines you use where you clamp various workpieces, welding rotators rotate, twist, and turn workpieces automatically.
Is it Safe to Purchase Used Welding Rotators For Sale?
Just like any other item or equipment, it’s safe to buy welding rotators that have already been used.
An example of a welding positioner that has previously been used
However, you have to look at too few factors about what you’ll purchase, too. These factors include:
Status or Condition of Welding Rotator
Check the wheels of the welding rotator and see if it’s already worn out. Although this particular component is replaceable, it’ll still add up to your costs, right?
One way to determine if the wheels are in good status is to rotate it without a workpiece. If it jitters and vibrates, you might have to look at the gears behind it. Otherwise, they’ll be good to go!
How the Welding Rotators Are Used
Many companies and businesses overuse welding rotators by using it other than their primary purpose. For instance, if they’ve been used for heavy-duty applications where the weight and the size of the workpiece exceed the threshold of the rotator, there’s a big possibility that its gears are already worn out.
Price and Rate
You can also check and assess the rate and the price of the used welding rotator. Try to place it side-by-side with a brand new welding rotator and observe if the price difference is substantial.
If it is, conduct a thorough inspection of all the parts and assess their condition.
That brings us to our next question, which is…
What Are the Parts of a Welding Rotator?
Image where you can clearly see the parts and components of welding rotators
The traditional welding rotator is comprised of two (2) parts:
- Idler supporting unit
- Motorized drive unit (power)
When dissected, each of them would have different parts, too!
Idler Supporting Unit
The idler support, or more commonly referred to as the “base” is the part that carries the wheels or the mediums that perform the rotation or the twisting of the workpiece.
Parts of the idler supporting unit include:
- Drive turning roll
- Driven wheel frame
Motorized Drive Unit
Akin to the idler supporting unit, the motorized drive unit is also comprised of different parts and components.
For the benefit of everyone, the motorized drive unit is the part of the rotator that gives off the power and the energy to make the welding rotator work.
The controller and the motor are two (2) of the most important parts of the motorized drive unit.
These are the parts of a welding rotator. Some welding rotator manufacturers and suppliers might add too few parts and components to complement it, but these are the parts of a traditional rotator.
Welding Rotators vs. Welding Positioners
Now comes the big question – the question that almost everyone gets confused at. What’s the difference between a welding positioner and a welding rotator?
A sample image of what a welding positioner looks like
A welding rotator is a type of machine that can help automate your welding. You can use it for items and workpieces that are cylindrical or round in shape to rotate, twist, and spin it automatically, allowing the welding head to be stagnant in just one (1) position.
On the other hand, a welding positioner is an auxiliary welding equipment that can rotate, reposition, and realign the workpiece. With a welding positioner, it can allow the welder to just remain in a single place while welding, without going back and forth to achieve the desired position.
Welding rotators rotate workpieces, parts, and components; welding positioners reposition it so that the welder exerts less effort.
What Welding Processes Are Capable of Utilizing Welding Rotators?
Submerged arc welding or SAW can go and function well with a welding rotator
You can utilize welding rotators to complement and assist a ton of welding processes, which include, but are not limited to:
Should you choose to utilize a welding rotator to finish any of these processes, you can expect faster, more accurate, more precise, and higher quality products.
Is There a Manual Adjusting Welding Rotator?
Manual adjusting welding rotators don’t necessarily mean that it requires human interaction.
Welding rotator that’s manually adjusted – without a controller or a power box
Instead, manual adjusting welding rotators are rotators that do not have computer numerically controlled or CNC capabilities.
What this basically means is that workers would have to adjust the speed, frequency, as well as the height of the rotators manually by inputting it to the control system.
That’s the true definition of what a manual adjusting welding rotator is.
And to answer the question, yes, you can purchase a ton of manual adjusting welding rotators. As a matter of fact, they are even recommended more by experts and specialists because of the amount of control you that you have over it.
Welding Rotator Applications
You can use welding rotators in a wide array of applications and business sectors.
Storage and pressure vessels are among the most common parts produced through the help of welding rotators
However, the most common applications you can have of it include the welding of:
- Storage Tanks
- Water Tanks
- Shipyards and Ship Components
- Pressure Vessels
Different Types of Welding Rotators
As opposed to what many people believed initially, welding rotators isn’t just limited to a single model of a machine.
Fit up welding rotator – one of the most customary kinds of welding rotators
In fact, there are several other types and kinds of welding rotators in the market today. Some of the most common of these types include:
Adjustable Turning Rolls
These are the welding rotators where their turning rolls are easily adjustable to fit the girth and the width of the workpiece or the material you will be welding.
Fit Up Welding Rotators
Akin to adjustable turning rolls, fit up welding rotators adjust to fit the size of the workpiece. This is to ensure the accuracy and the precision of the weld.
Pipe Pinching Rotators
Pipe pinching rotators, from its term alone, is a type of welding rotator that clamps onto a pipe or any type of cylindrical object, assisting to carry them out for automatic welding.
These machines are the best and the most ideal for solving the problems of tilting or rotating pipes and other materials of the similar state, size, and dimensions.
Self-Aligning Welding Rotators
From the term alone, you would already know what self-aligning welding rotators are.
They’re welding rotators that are automatic when it comes to aligning the workpieces, for them to be balanced.
Most self-aligning welding rotators contain two (2) units that continuously arrange and align workpieces.
These are some of the most common types of welding rotators you can purchase in the market!
Welding Rotators vs. Welding Turntables
Akin to what welding positioners are, welding rotating tables or welding turntables also aid in whatever welding processes you want and need.
A sample image of what a welding turntable looks like
It’s easy to differentiate the two (2). As a matter of fact, here’s how you can determine it.
Welding turntables are tables that spin, rotate, or twist in whatever 360-degree direction you want it to face.
It’s easy and simple to differentiate them because welding rotators would usually have wheels to assist in the rotating or the spinning of the cylindrical workpiece. Turntables, on the other hand, are tables that assist in the spinning or the rotating of the workpiece.
What Are Benchtop Manual Welding Positioners?
Benchtop welding positioners are like small versions of large welding positioners.
Sample image of what a benchtop manual welding positioner is
They’re dubbed and labeled as “benchtop” because of the work desk that it has. In addition to that, it’s labeled like that because it can easily be mounted on top of a sturdy plain top.
What Are the Benefits and Advantages of Using Welding Rotators?
You can get a ton of benefits and advantages of using welding rotators for your projects.
Some of these most common beneficial and advantageous instances include, but are not limited to:
Increased and Heightened Productivity
One of the primary benefits and advantages of using welding rotators is that you get heightened and fully developed productivity.
Because you wouldn’t be meddling with the workpiece, your welders can stay in one position and perform the weld. This can actually be efficient and effective in promoting your overall productivity.
Your Welders and Workers Are Safer
Imagine your welder carrying, turning, and manually handling a 100-kg tank vessel, wouldn’t that be dangerous to the safety and the security of your workers?
With a welding rotator, though, you don’t need to worry or think about manually handling workpieces; you can mount them onto the welding rotator so they’ll move, rotate, and spin automatically.
Higher Quality Welds
By automating the movement or the rotation of the workpieces, you can be sure that the quality of the welds will be higher, more accurate, and more precise.
9 times out of 10, the entire weld will 100% match the plan and the results you are expecting to get.
Do note, though, that these benefits and advantages are only some of the most common and the most customary. There are other advantageous and beneficial things you can get if you use welding rotators.
And while these benefits and advantages seem impenetrable, there are drawbacks to using them as well.
That brings us to our next point, which is…
What Are Disadvantages of Using Welding Rotators?
Yes, using welding rotators aren’t all rainbows and butterflies; there are other disadvantages to them as well.
As a matter of fact, you need to consider them because they usually form large parts of projects.
Technology Requirements
Part of the cons of using welding rotators would be the requirements of the technology.
Contrary to popular belief, welding rotators would only be highly effective if they’re used complementarily with other welding equipment like a column & boom welder, a welding positioner, a robotic welding head, etc.
You can manually weld, but it wouldn’t be that efficient – it can provide promising safety and security to the worker, yes. However, it might not be as efficient as you think.
Only Effective in Materials With Good Weldability
Another drawback you’ll most likely experience is the fact that it can only work on materials and substances that have extremely good levels of weldability.
In metallurgic work, these are steels and a couple of alloys – but not all of them. So, be sure to check out the material that you’re going to weld.
Experience Requirement
Last but definitely not least would be the requirement of experience from the welder.
Even if the welder plans on automating it by using a welder machine, that particular welder would need experience to know where more work is required, where they need to concentrate more, etc.
These are some of the major drawbacks of using welding rotators.
Automatic Welding Definition
Automatic welding is a slightly general term for welding procedures that utilize machines and equipment that performs continuous welding without human intervention.
Sample image of semi-automatic welding where the worker slightly adjusts the welding head
You can think of the comparison as a manual transmission car and an automatic transmission car. In a manual setting, the operator would need to exert effort in making the weld accurate, as well as in positioning it.
On the flip side, automatic welding will be capable of running continuously without the need of human intervention.
Are Welding Rotators Part of Automated Welding?
Ideally speaking, yes, welding rotators help in automating welding procedures. How? – By handling, twisting, rotating, and maneuvering the workpiece without the need of an operator.
Of course, this is considering the fact that other welding equipment and machines are in place. For instance, if it works side-by-side with a welding manipulator, then you can consider it a part of the things that help automate welding.
How Much Do Welding Rotators Cost?
Welding rotators vary in price depending on the manufacturer, the features and functionalities they have, and the like.
But, to give you a generic and a rough estimate of how much they are, welding rotators usually cost anywhere between $8,000 and $30,000.
Other factors that can affect the price includes:
- The amount or the volume you’ll be purchasing
- Where you are (shipping and freight costs)
- Add-ons or complementary factors you want to include
In finding good welding rotator manufacturers, what do you need to keep in mind?
How to Find the Best Welding Rotator Supplier
Landing on the best welding rotator manufacturer is always tricky. Apart from the fact that almost all manufacturers today offer the same deals, anyone can easily be deceived by fakes and counterfeits.
For you to avoid it effectively, you can refer to the following points:
Check Reviews and Client Feedback
One of the foolproof ways of determining whether or not a welding rotator supplier is reliable is by checking what their previous clients have to say to them.
Most, if not all welding rotator suppliers post their clients’ feedback on their website. This is to front what other businesses have to say to them, as well as to give future clients the assurance that they are legit.
It’s a good platform that you can start to look at in determining whether or not a welding rotator manufacturer is trustworthy or not.
Try to Contact the Welding Rotator Manufacturer
You wouldn’t actually know anything about a supplier unless you contact them.
By giving them a buzz, you can determine too few factors about how they do their business. You can check and assess their level of urgency by noticing how fast they respond to messages and inquiries; you can have a feel of what it’s like to do business with them; and many more!
A single conversation with them can help you grab a feel on what it’s like to work with them.
Check Their “About Us” Section
Last but definitely not least is by checking their website and navigating to the About Us section that they have.
This section can be the literal game changer of your patronization. If you deem that they’re excellent in terms of doing what the do best, don’t hesitate to give them a call.
On the other hand, if you weren’t able to find what you were looking for, try contacting and initiating a conversation with them.
You don’t really have to spend hours background checking companies to know if they’re legitimate or not. By doing these three (3) things, you can shave off hours of you inspecting and checking everything.
Where Can You Find High Quality Welding Rotators?
There are a ton of welding rotator manufacturers you can work with in the market.
But, have you heard of Chinese welding rotator suppliers? Not to burst your bubble, but welding rotators from China are actually the best, the most reliable, and the most trustworthy.
Apart from the fact that you can get it for the best and the most competitive price with them, you’ll also be able to build relationships with other suppliers in the future.
But out of all Chinese welding rotator suppliers out there, nothing beats Weld Fab. For years on end, Weld Fab has been the most sought-after supplier and manufacturer of welding rotators in the Chinese market.
We’re considered the best as we are partnered with many world-renowned companies.
Can You Trust Weld Fab’s Welding Rotators?
Being the best in the welding rotator manufacturing and production industry, yes, it’s safe to say that you can definitely place your full trust in Weld Fab for all your welding rotator needs.
Our company was successful in combining research & development, to sales, marketing, and even the inculcation of advanced machinery and equipment.
Wherever country you are in and whatever type of business you’re involved in, you can always bank and trust us here at Weld Fab to guide and assist you!
Other Products We Offer
Apart from our welding rotators, you can also entrust the production of other welding equipment to us such as CNC gantry milling machines, drilling machines, lathes, welding positioners, and many more!
We’re equipped with the most skilled, experienced, and adept staff members comprised of experts and professionals in the electrical, welding, production, and even assembly sectors!
What Welding Rotators Can Weld Fab Offer?
Weld Fab is one, if not the most comprehensive welding rotator supplier in the country. We’re skilled and more than capable of providing and supplying all types of welding rotators from conventional and traditional welding rotators, self-aligning welding rotators, drift – to fit up rotators, and many more!
You will never experience a shortage of what you need when you decide to work with us here at Weld Fab!
Contact us today and we’ll offer you a good price! Not only that, we’ll immediately give you a free quotation or a free estimate of all the products you need!